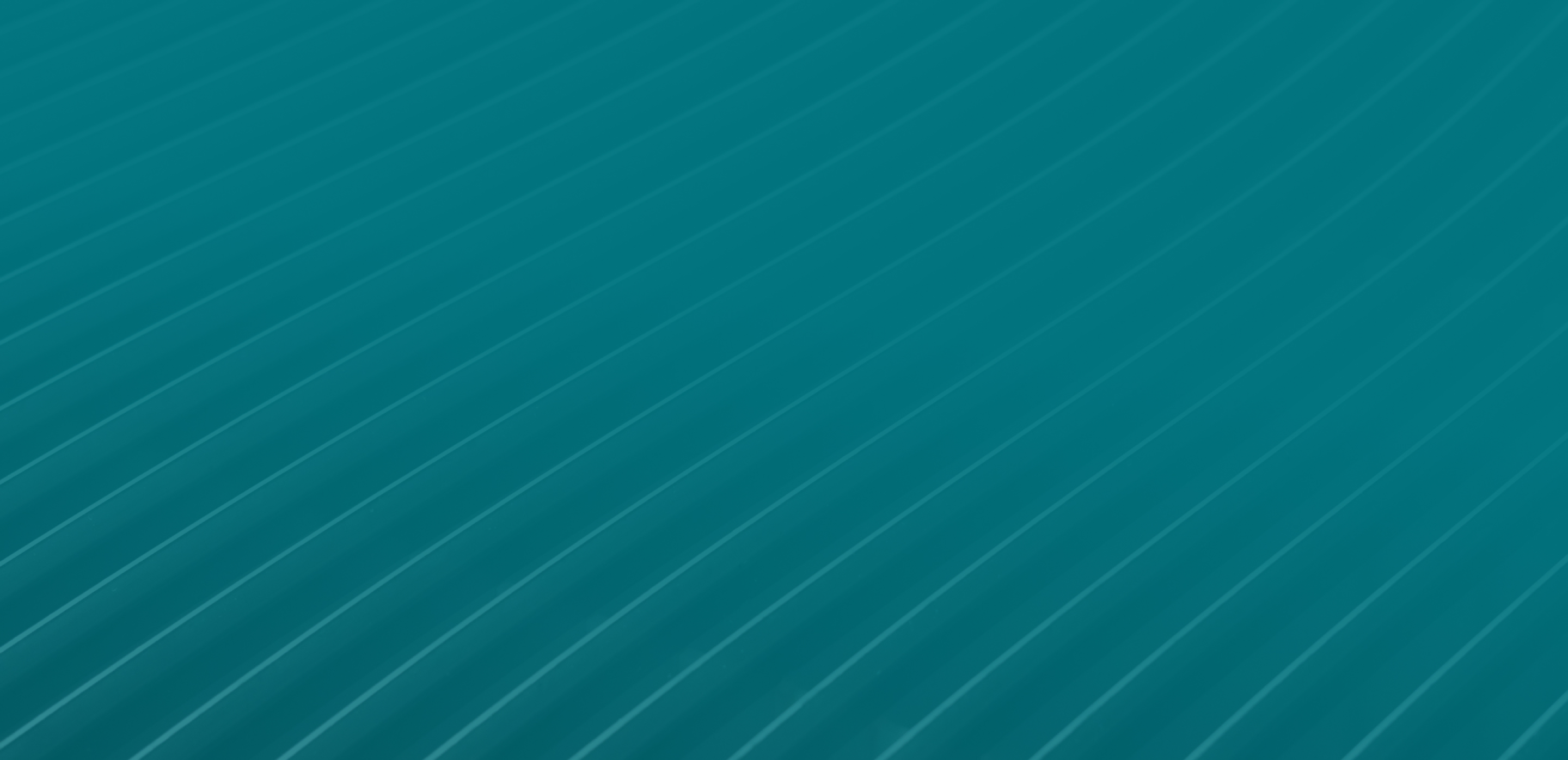
Waterjet
Dictionary
Waterjet terms might seem unusual if you are new to the technology.
Review waterjet technology definitions (from the everyday to the obscure), so you can feel confident in your waterjet know how. Expand your waterjet knowledge with the waterjet dictionary.
A-F
Abrasive Mesh Size
Abrasive Waterjet
Abrasive Waterjet Attributes
- Extremely versatile process
- No Heat Affected Zones
- No mechanical stresses
- Easy to program
- Thin stream (0.020to 0.050 inch in diameter)
- Extremely detailed geometry
- Thin material cutting
- Over 12+E7 inch thick cutting
- Stack cutting
- Little material loss due to cutting
- Simple to fixture
- Low cutting forces (under 1 lb. while cutting)
- One jet setup for nearly all abrasive jet jobs
- Easily switched from single to multi-head use
- Quickly switch from pure waterjet to abrasive waterjet
- Reduced secondary operations
- Little or no burr
Check Valve
As an example, low pressure water comes in through a typical low-pressure hose and enters the pump awaiting pressurization. Once pressurized, that water is not allowed to exit through the low pressure check valve because it would immediately burst the low-pressure hose. Instead, another check valve opens to allow the high-pressure water to be safely routed out the high pressure stainless steel lines on its way to the cutting head.
Composite CFRP
Today's lightweight advanced composites can be as hard and rigid as steel, or as flexible as rubber, and still hold up to the stresses of supersonic flight. The same properties that make these materials so tough also make them extremely difficult to cut. Composite technologists continue to introduce new material combinations that defy the capabilities of traditional machining methods.
Until recently, conventional cutting methods, diamond or carbide-tipped mills or routers, band saws, cutoff saws and abrasive wheels were used to cut these unconventional materials. Due to the composition and fiber orientation of advanced composites, conventional cutting methods damaged the composites either by heating them up or by leaving frayed or delaminated edges. In addition, these methods were often slow, frequently leaving behind delamination and other issues requiring costly rework.
Composites can come in many forms. High temperature engines use metals reinforced with ceramic fibers (metal matrix composite). Typically, engineers are seeking to reduce weight while delivering higher strength, greater flexibility, or temperature resistance. These materials give production shops fits, yet they can be cut with speed, precision, and material integrity on a Flow waterjet.
Control System
To further explain; an engineer or designer might draw a square to be cut on a waterjet within a CAD (computer aided design) program such as AutoCAD®. A programmer (might be the same person) then takes that square drawing as a .dxf or .dwg file type and brings it into a CAM (computer aided manufacturing) software package.
Here, the programmer adds in the waterjet start stop locations, direction of travel, cutter compensation, and travel velocities necessary. This file is then sent to the control system where the operator (again, could be the same person) opens up the file in the machine tool control system, locates the cutting head in the start position over the target material, and presses cycle start to cut the part.
The control system then turns the cutting file into electrical current going from the control system drives to the machine tool motors to move the machine around. The control system also fires off digital outputs to start and stop the water and the abrasive automatically.
Cutting Head
In abrasive waterjet cutting, the cutting head also includes the mixing chamber and mixing tube. Sometimes you will hear of the cutting head also including the on/off valve. This valve resides just above the orifice and utilizes some type of poppet and seat configuration to allow the operator or the CNC controller to start and stop the waterjet stream.
Cutting Power Density
Direct Drive Pump
Drive Motors
Dynamic Waterjet
In waterjet cutting, the jet creates two errors when cutting a part at high speed: stream lag and taper. Stream lag is where the stream exits the workpiece behind the entrance point. Taper is V-shaped. Both stream lag and taper can be minimized by slowing down (usually to 15 to 20% of maximum cut speed) but cannot be eliminated.
To enable high speed cutting, Dynamic Waterjet automatically angles the head to one side so that all the taper goes to the scrap side, and slightly tilts the head forward to compensate for stream lag. This taper and stream lag compensation takes place automatically in a behind-the-scenes operation. The operator or programmer do not need to program the angles, the control system takes care of it. The angle even changes automatically with cutting speed, so precision corners and arcs can be created as the cutting head changes speed to negotiate corners.
Dynamic XD
E-stop
Feedback System
The higher the drive, motor, and feedback resolution the more precise the waterjet cutting head motion will be. Feedback systems can be encoders attached to the motors, tape scale or glass scale attached to the machine frame in direction of travel, or other means.
G-K
Garnet Abrasive
High Pressure Plumbing
HyperPressure
Intensifier Pump
The “intensification principle”, or ratio, uses the difference in biscuit/plunger area to intensify, or increase the pressure. Hydraulic oil is pressurized and the low-pressure oil pushes against a biscuit, which has a face area 20 times greater than the face of the high-pressure plunger that pushes against the water. Therefore, the pressure is “intensified” twenty times. E.g., 3,000 psi of oil pressure will generate 60,000 psi of water pressure due to the 20:1 ratio of biscuit area to plunger area.
Jewel Orifice
Orifice size does not dictate maximum water pressure - only horsepower and pump design determine max pressure.
The top of the orifice has a very sharp edge so that the waterjet stream is coherent. A rough or rounded edge will create a fuzzy, turbulent jet and may exhibit an angular trajectory that is not desired.
An orifice blows out in waterjet from two primary causes. First, calcium can build up on the orifice and break off, causing instant orifice failure. Second, the orifice edge can become rounded or break from particle impact. In waterjet, an orifice is usually either good or bad - gradual degradation is less common. Sapphire and ruby orifice can last 40 to 200 hours, depending on application and pressure, with good water. A diamond might be 8 to 10 times more expensive but will last 8 to 10 times longer.
Kerf
So, for a 0.030" mixing tube, the kerf will be 0.033" Of course, the kerf will increase as the mixing tube grows. Tube growth is about 0.001" per 8 hours of jet-on time.
A waterjet's thin cutting width is a major attribute, allowing intricate detail. A pure waterjet stream ranges from 0.003" to 0.015", and an abrasive waterjet from 0.015 to 0.070" (typically 0.040")
L-P
Mixing Tube
The supersonic waterjet stream then enters the mixing chamber where the abrasive is pulled into the head via a venturi effect. Then the water and the abrasive pass through the mixing tube and exit as a mixture of water, abrasive, and some air.
The mixing tube can range from 0.015" to 0.070" in inside diameter, and 1.5 to 6" long. It has an internal entrance cone. The most common mixing tube is 0.040" inside diameter and 4 inches long. This tube would typically use 80 mesh garnet abrasive. In normal cutting a mixing tube of high-quality material (nano-grained composite carbide with very little binder to maximize erosion resistance) wears at approximately 0.001" diameter growth per 6 to 8 hours of run time, and also wears concentrically.
Part Accuracy Characteristics
The waterjet beam is not rigid but can bend and move in the material. The waterjet stream parameters and non-rigid characteristics can affect part accuracy, such as stream lag, V-shaped taper, abrasive flow rate, etc. Controlling these characteristics has been the focus of waterjet suppliers for many years.
Dynamic Waterjet® automatically compensates for stream lag and taper allowing for 2 to 4 times faster cutting and finished part tolerances of 1 to 3 thousandths of an inch.
Programming Software
Programming software is also called CAM software (computer aided manufacturing). Programming software is usually on a PC, though machine tools can also be programmed right on the machine. A programmer imports a previously created CAD drawing as a .dxf or .dwg file type (or other format) or creates the pattern anew in the CAM software package.
A programmer uses the programming software in waterjet to add start and stop locations, direction of travel, cutter compensation, and travel velocities necessary. This file is then sent to the control system to be executed in cutting the part.
Pure Waterjet
Pure waterjet can also be used to remove coatings, such as paint off ships, if you are interested in learning more about these applications click here.
Pure Waterjet Attributes
- Very thin stream (0.003 to 0.010 inch in diameter is the common range)
- Extremely detailed geometry
- Very little material loss due to cutting
- Non-heat cutting
- Cut very thick
- Cut very thin
- Usually cuts very quickly
- Able to cut soft, light materials (e.g., fiberglass insulation up to 24" thick)
- Extremely low cutting forces
- Simple fixturing
- 24 hour per day operation
Q-U
Stream Lag
Stream Velocity
Once the stream exits the orifice, it's all about velocity. There is no pressure in the stream after the water passes through the orifice.
In abrasive waterjet cutting the faster the stream, the quicker the abrasive moves, the faster the cutting, the smaller the diameter of the stream, and the less abrasive is required.
Taper
Transition Zone and Striations
Ultrahigh-pressure (UHP)
V-Z
Venturi Effect
Abrasive is pulled in by a venturi effect into the mixing chamber and accelerated like a bullet out of a rifle, or shot gun pellets in a shot gun, out of the mixing tube, thereby creating the abrasive waterjet.