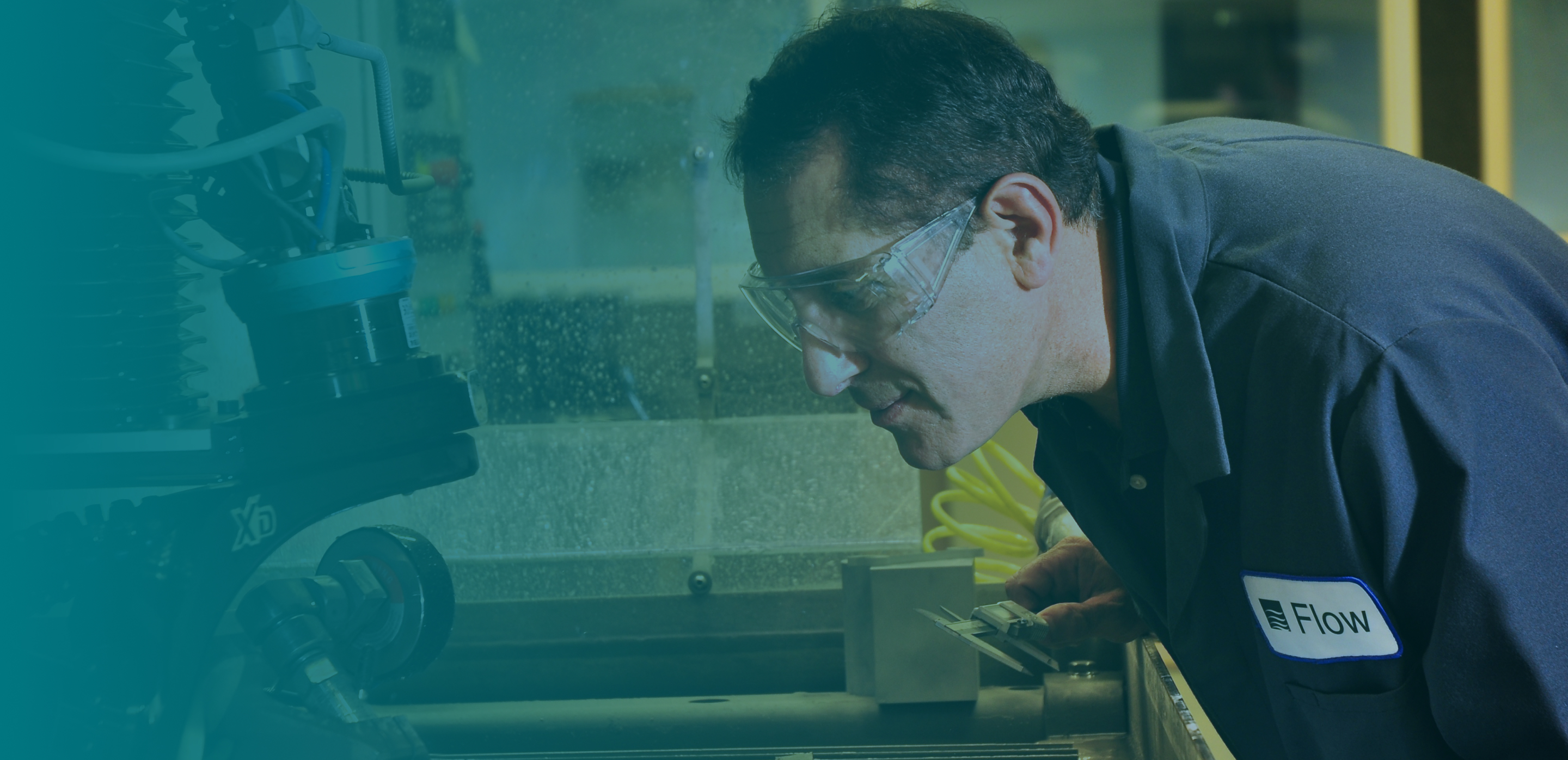
Ask
Dr. Hashish
Dr. Mohamed Hashish led the Flow team of engineers in the 1970’s who invented the abrasive waterjet. Dr. Hashish is a world leading expert in high pressure design (with over 45 patents) and tribology, and quite frankly, one of the nicest, most brilliant people you will meet. Even with his mountainous list of credentials, he’s willing to answer your personal waterjet questions. It doesn’t get much better than that.
Benefits
What are the benefits of purchasing a waterjet compared to a CNC plasma or a laser?
Good question, but the answer isn’t quick. Bear with me please as I step though some comparisons.
Versatility
Abrasive waterjet can cut almost anything – from metal to stone to glass to composites to ceramic. Abrasive is used to cut those materials. Then we can switch to pure waterjet, without abrasive, and cut soft goods that can be cut with a knife, such as plastic, foam, gaskets, food, paper, and (if the pressure is high enough) even shim stock aluminum.
Laser and plasma cut with heat, and so can only cut materials that have the right thermal properties. Metal is almost always the target material in industry for these heat-based processes. And mild steel is almost always the metal that is cut by them. In addition, plasma can only cut things that are electrically conductive. To optimize laser and plasma cutting, change to gasses is required. No change to waterjet parameters, except speed, is usually required for any material.
Thickness
Abrasive Waterjet can cut very thin and up to 12 inches (sometimes more) of any metal, glass, stone, composite, etc. Most precision cuts are made with our Dynamic Waterjet at thicknesses of 4 inches or less, but rough cutting is possible for thickness well beyond 4 inches. Laser and plasma are not as versatile in thickness. They cut like a camera, only on that which they can focus on. Laser cuts very thin and up to ½ inch, with large CO2 lasers getting up to 1 inch thick today. Plasma cuts from about ¼” up to 1.5”. Beyond that thickness, shops usually switch to oxy acetylene to go up to 8” as it will cut faster and thicker than plasma.
Edge Finish
Nothing cut by a plasma or laser will be as high of quality of an edge as a waterjet. Waterjets leave behind a smooth edge. No heat affected zones or mechanical stresses are introduced. That means you can have a smooth edge that does not require any grinding or finishing. Because it's a cold-cutting process there is no slag, dross, or change in material properties. The plasma and laser cut with heat (waterjets cut with supersonic erosion). Plasma and laser therefore will leave behind heat affected zones, mechanical stresses, and, especially with plasma, dross 'drips' on the edge. Laser can minimize this heat affected zone and stress but can’t eliminate it. That is why heat cutting is not allowed on any aerospace parts unless you completely grind away the heat-cut edge.
So, is waterjet better for everything?
No. When cutting mild steel thin sheet metal, say 12 gauge, the laser will cut faster and cheaper. We can stack to come closer to laser speed, but we cannot equal it (yet). So, for high production runs where set up time is not a problem, laser will cut your thin mild steel sheets faster. And you might stick with plasma if you’re cutting, again, mild steel ½" thick and you don’t need to grind away the heated surface for either cosmetic or strength reasons. In this case our waterjet will be more costly.
But waterjet is the fastest growing machine tool process in the world (per Frost & Sullivan) because it is so incredibly versatile (cut anything that comes into your shop), quick to set up (same parameters cut almost everything with just cut speed change), leaves the best edge (no heat, no stress, satin smooth), and are easy to run (software models make it really easy to program and start cutting). If you have more than mild steel in your shop, you probably need a waterjet.
What is the most important benefit of a waterjet machine?
There are many benefits when using a waterjet, it is difficult to narrow them down to just one. There are two equally important benefits to waterjet that separate it from other machine tools; versatility and no heat affected zone.
Versatility: Flow waterjets enable you to cut a variety of material with ease using a single machine. Metal, stone, plastic, composite, glass, ceramics, and more can all be cut with a single Flow Waterjet. The same system can also cut a variety of thicknesses – most Flow Waterjets can cut up to 8" thick.
No heat affected zone: Waterjet cutting is a cold-cutting process. Heat can have a negative effect changing the structure and properties of metal alloys. Waterjet cutting is high-speed erosion which does not affect the structure and allows for many layers to be cut simultaneously.
Applications
In addition to hard materials such as steel, can a Flow waterjet also cut soft materials such as carpet?
Can a waterjet cut 24” of stone that is square, circle, or tapered?
Absolutely! Waterjet cutting is high speed erosion focused through a tiny, jeweled orifice with pressures up to 94,000 psi.
Waterjet allows for highly intricate designs, inlays, and mosaics in stone – no other cutting technology is better suited for intricate stone cutting than waterjet.
Before cutting on a waterjet, do you have to pre-drill holes?
Can a waterjet cut Tungsten metal?
Although Tungsten metal is extremely hard, it can be cut using a Flow Waterjet!
Flow Waterjets are one of the most versatile machine tools, cutting everything from baby diapers to very hard materials like Tungsten!
How well would a unit be at cutting CAD designed pieces of 3" thick memory foam?
What is the hardest material that a pure waterjet can cut?
When etching, how is the lead in/out set without ruining the design?
When etching with a Flow Waterjet draw your lead-ins and lead-outs in FlowMaster on a line in the design with no offset.
That should let you etch without ruining your design.
Will it cut 1/2" stainless steel plate?
Abrasive waterjets can cut nearly any material, including stainless, from 1/16" to 8" thick. Typical part tolerances range from 0.003"–0.005", and up to 0.001" in some applications.
Cutting ½" stainless can be done at 7–30 inches per minute depending on the waterjet’s operating pressure and the desired edge quality.
Wouldn't your models be too much (dollar cost/unit) for production cutting items like diapers, paper, foam, and gaskets?
Technology
At what pressure do you cut?
You want to cut at the highest pressure available to you so you can maximize your cutting speed and minimize the cost per part. The higher the pressure, the less need for abrasives and thus lower overall cost of operation, in spite of the slight increase in the pump maintenance cost.
94,000 psi is the maximum commercial intensifier rated pressure today for highly reliable operation at 87,000 psi.
Can the length of the waterjet stream be controlled?
Does the nozzle ever wear out? What material is it made of to withstand such pressure and erosion?
Yes, the nozzle on the machine does wear out. The mixing tube is where the abrasive and ultrahigh-pressure water mix together then exit to perform their cutting duties.
These tubes are made of Carbide and can last up to 2.5 weeks, depending on actual use, type of abrasive, etc.
Many variables come into play when calculating the life of mixing tubes. As the mixing tube wears, it becomes larger, allowing the water to fan out more, causing a less accurate cut.
In some cases, this is not a problem, but in high-precision work it is necessary to routinely check the mixing tube for wear. Most waterjet users do not discard their worn mixing tubes, they use them for rough cutting or low-precision work.
I realize RO water may be too aggressive. What makes nano-filtration water too aggressive for the Intensifier?
We recommend against de-ionized (DI) water as it is too aggressive. We do have customers that use reverse osmosis (RO), but in most situations RO is an unnecessary precaution for waterjet cutting.
I have spoken to several associates and there is little experience in nano-filtration. I do not believe that nano-filtration is too aggressive, but it, too, might be an unnecessary precaution, but we would need more data to completely understand the process.
At our Customer Technology Center in Kent, Washington we run a double filter system of 1 micron and 0.5 micron filters from local tap-water. At times Flow recommends water softeners for customers who have hard water. This prevents deposits building on the orifice.
If there are concerns about your local water quality, I would recommend performing a water quality test. This is done for all Flow customers before they purchase our equipment.
What happens when I stick my hand in the jet stream?
What is the difference between a 60 hp pump verse a 120 hp pump?
A 120-horsepower pump will have a higher maximum flow rate of water versus the 60 hp, which may let you cut faster.
Keep in mind that any increased cutting speed is a result of pumping more water and abrasive through your orifice, which increases your operating cost and wears out your orifice faster. If you're looking for more cutting speed with lower operating costs, higher psi is more effective than increasing horsepower.
Flow's 94,000 psi pumps achieve higher cutting speed with less water and abrasive than our 60,000 psi pumps. Pressure = Productivity.
What kind of abrasive are you using?
Garnet is by far the most commonly used abrasive material. Users have found garnet to be the best for them in terms of cost, cut speed, mixing tube life, and health hazards.
Other abrasives include olivine sand, aluminum oxide, and some man-made materials.
What stops the waterjet from cutting through the tank to the floor?
What type and how much material can you stack on each other to get a good finish size? (Dynamic head 30 hp Hyplex)
Stack cutting with a Flow waterjet can save you time and money if the application is right.
The best range of stacking is .400 to .600 inches. The higher the stack the slower the cutting. Stacking is best for thin material – say a .125 piece can be cut in 3 minutes but stacking 4 high/.5 inches it will cut in 8 minutes taking the cut time down to 2 minutes per piece. If I stack 8 high it will now take 32 minutes to cut or 4 minutes per piece.
The edge quality will still stay the same as if you’re cutting .500 inch or 2 inch since 20% speeds will change based on thickness. At higher speeds, 60 to 80% the bottom pieces will be rougher than the top pieces.
Although it is certainly possible to stack 2" or even more, the effect of worse edge finish and striations become more apparent as the stack gets thicker. The only remedy to this would be to slow down the machine to help ensure that the bottom pieces of the stack have an acceptable edge finish.
As a result, the overall cycle time may increase to the point where it's not worth stacking in the first place.
As mentioned before, the most effective total stack thickness would be around 0.400–0.600 inches. Up to this thickness, there is still significant energy available in the cut stream as the jet exits the bottom of the material, maintaining a reasonable edge finish for the whole stack.
Beyond this thickness, it takes exponentially more time to maintain a consistent edge finish.
Software
What is the 3D software being used and where can I get professional training on a Flow Jet?
We have developed our own software suite for 3D cutting called FlowXpert. Flow partnered with SpaceClaim to develop the most advanced, yet easy to use waterjet software for 2D and 3D waterjet cutting.
Flow offers waterjet training for operation and maintenance. Our training facility is located in Kent, Washington. Contact: techtraining@flowcorp.com to inquire more or call 253.246.3300.