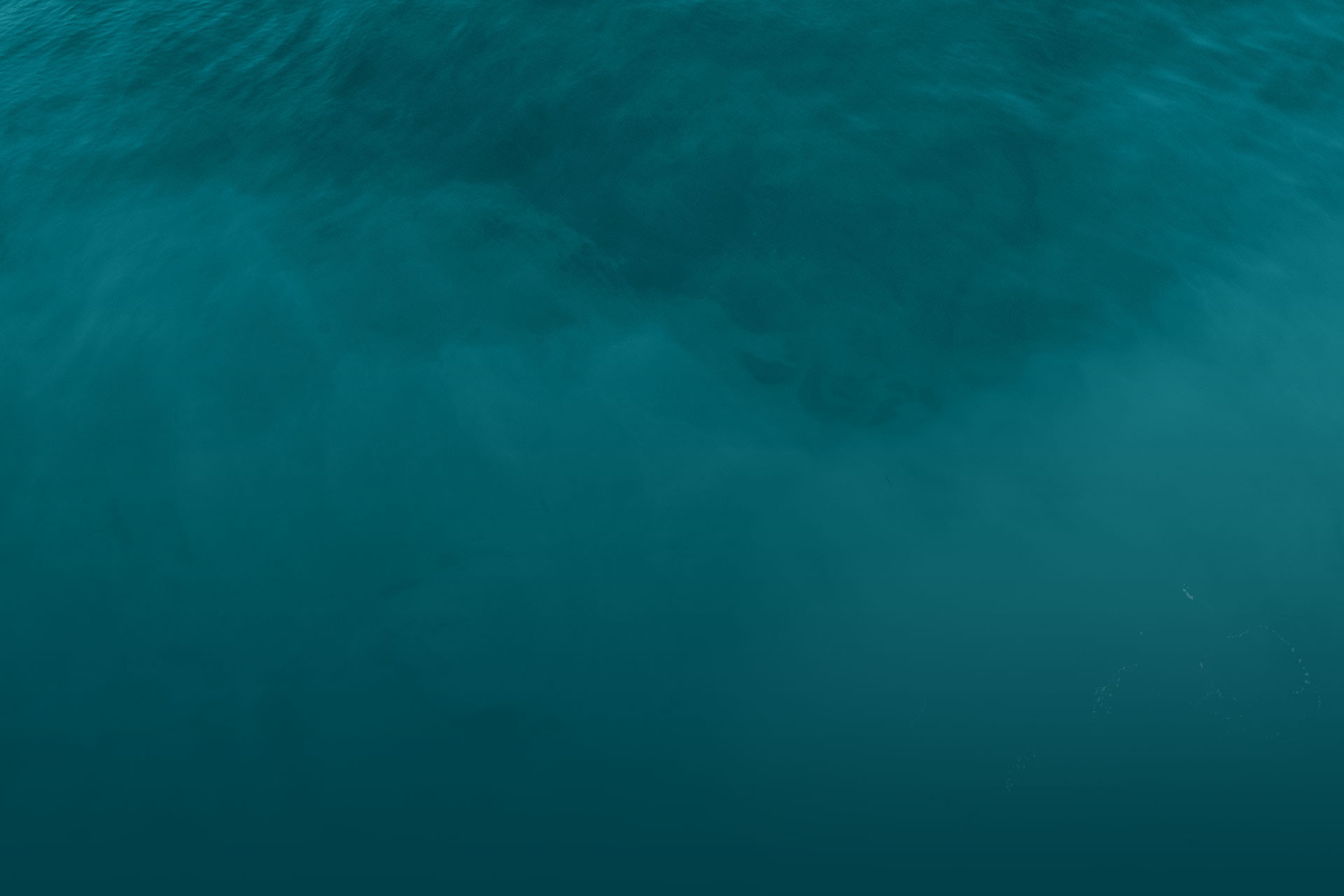
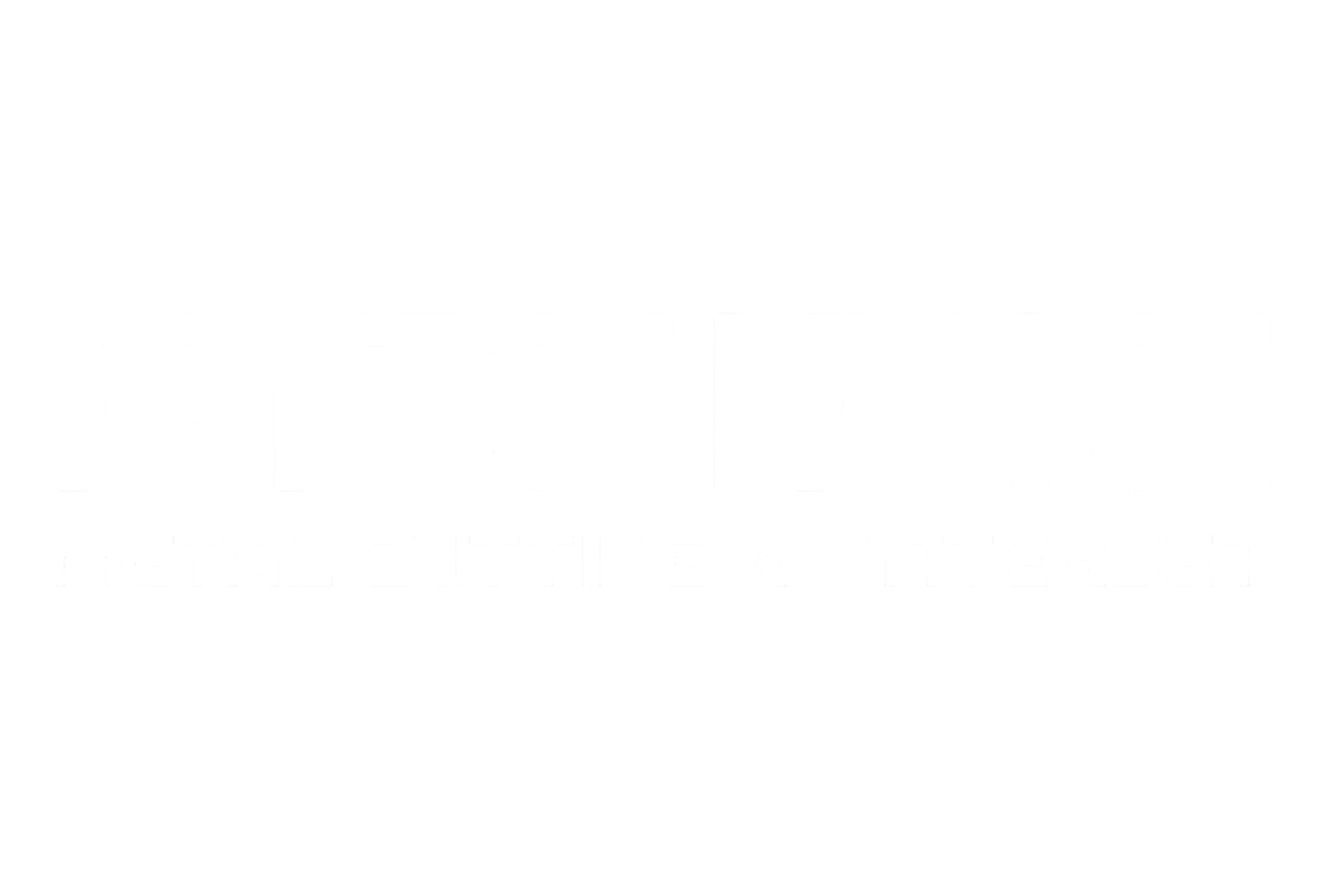
Becoming a Waterjet Powerhouse
Since its founding in 2002, Pacific Metal Cutting & Waterjet has transformed from a metal processing facility for distributors to one of the largest, high-capacity waterjet shops in the United States. Currently led by Matt McWhirter, the second-generation owner, Pacific Metal Cutting (PMC) is committed to precision and efficiency in their cutting services. Known for their innovative processing solutions and detail-oriented operations, it’s easy to see why they’ve grown as they have.
Pacific Metal Cutting & Waterjet
In the early years, they used only saws for their metal processing as they were readily available and less of a major investment. However, Mark McWhirter, Matt’s father, and first-generation owner and president, wanted to be able to do more than simple cut-to-size projects. Mark began researching how to expand into more complex cutting and broaden their capabilities, finding Flow waterjets along the way. In 2004 their first Flow waterjet was installed, an Integrated Flying Bridge (IFB) system, and their entire business model changed. They went from single-cut projects with required post-machining to a full-service shop offering complete products.
As the years went by and the shop grew, they invested in more Flow waterjets. “My dad was enamored by the technology when we visited the showroom. He knew Flow was what we needed from the start,” Matt says about their first waterjet. Matt took over as president in 2020, and by 2022, they were up to seven Flow systems – five of which were Mach 500 models equipped with HyperJet pumps.
“The ability to interchange parts if something goes down on one is a huge benefit. They have the same parts, training, software, and operation. It’s been a huge success having nothing but Flow systems in our shop.” - Matt McWhirter
Because they had continuity in system models, their parts were easily interchangeable, operating was seamless, and they could guarantee their cut quality every time. Since most of their clients are on long-term contracts that require extreme precision, keeping their systems running at their best is their highest priority. Parts must be right the first time, directly off the table.
While most of their clients are aerospace companies or metal distributors, they’ve also worked with local companies cutting wood, tempered glass windshields, and producing barriers during the Covid return-to-office era. Because of the versatility of their Flow, they’re able to cut materials ranging from .001” up to 12” thick including polycarbonate, titanium, and other metals. “We’ve become known for our creativity in our processing. We like to think outside the box on how to get things done, and have a wide material handling range, and quicker turnaround times due to the size of our shop,” Matt said. “Our business has completely changed since that first Flow. Our shop is up to two shifts now, with up to 19 hours a day with our waterjets operating. We’re considering a third shift to meet the demand.”
In 2024, after twenty-two years of being a loyal Flow customer, Matt and the Pacific Metal Cutting team invested in their eighth and ninth Flow waterjets – both Mach 500 systems with HyperJet pumps like the bulk of their existing systems. “The quality and technology from Flow is just hands-down the best. We’ve been happy all around with Flow and have continued to see improvements over the years. We wouldn’t recommend anyone else for a waterjet,” he said about his decision. “It’s not an easy job, to be a waterjet shop, but it’s very rewarding. I recommend doing your homework, and if you’re looking to be a waterjet-specific shop, make sure you get more than one.”