How Velocity Impacts Waterjet Technology
What makes a waterjet fast? It’s not what you think it is.
Long ago, man discovered the power of a sharp stone and its ability to cut. He also realized that by combining force (pressure) and striking objects with velocity (speed), he could break them. From this basic concept, many tools and weapons were created, and machine tools today still use this principle, with trends towards ultra-high speed and sharper diamond-tipped tools.Water was first recognized as a "soft" tool when rivers carved their way through the ground. In ancient Egypt, river branches were diverted to wash out soil in search of gold and other minerals. By the 19th century, higher velocity streams were being used for washing out and carrying ore from harder formations like coal. As profitable mining practices emerged in California, pumps were developed in the 20th century to obtain faster jets, leading to the introduction of waterjet cutting technology in 1970. The use of intensifier pumps allowed for the creation of high-velocity jets capable of cutting rocks and soft materials.
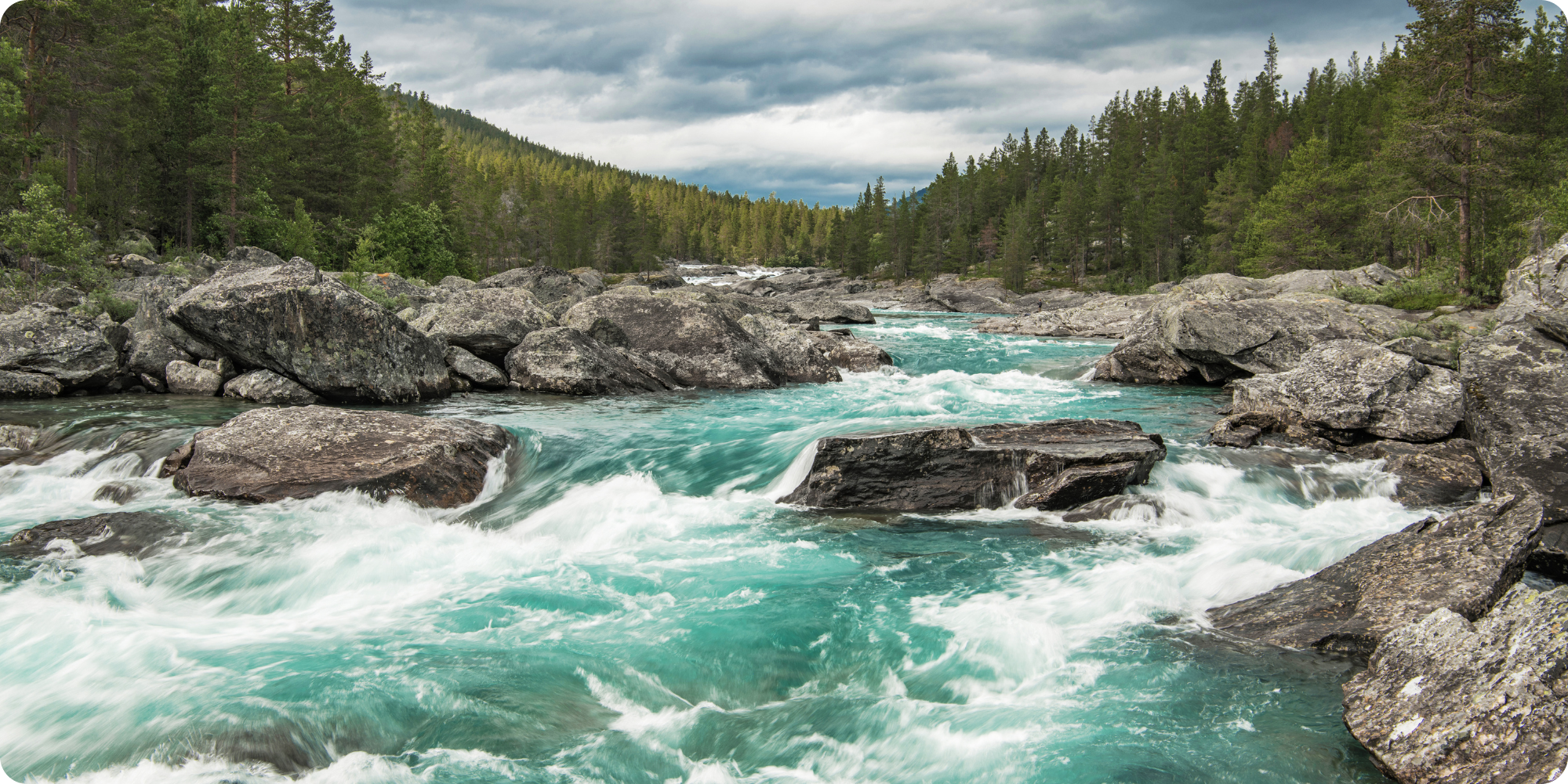
How Abrasive Waterjet Technology Works
In 1980, Flow stepped in to create high-velocity, sharp-edged particles capable of cutting metals and hard materials. This was known as Abrasive Waterjet (AWJ) and required higher-pressure pumps to achieve the desired abrasive particle velocities.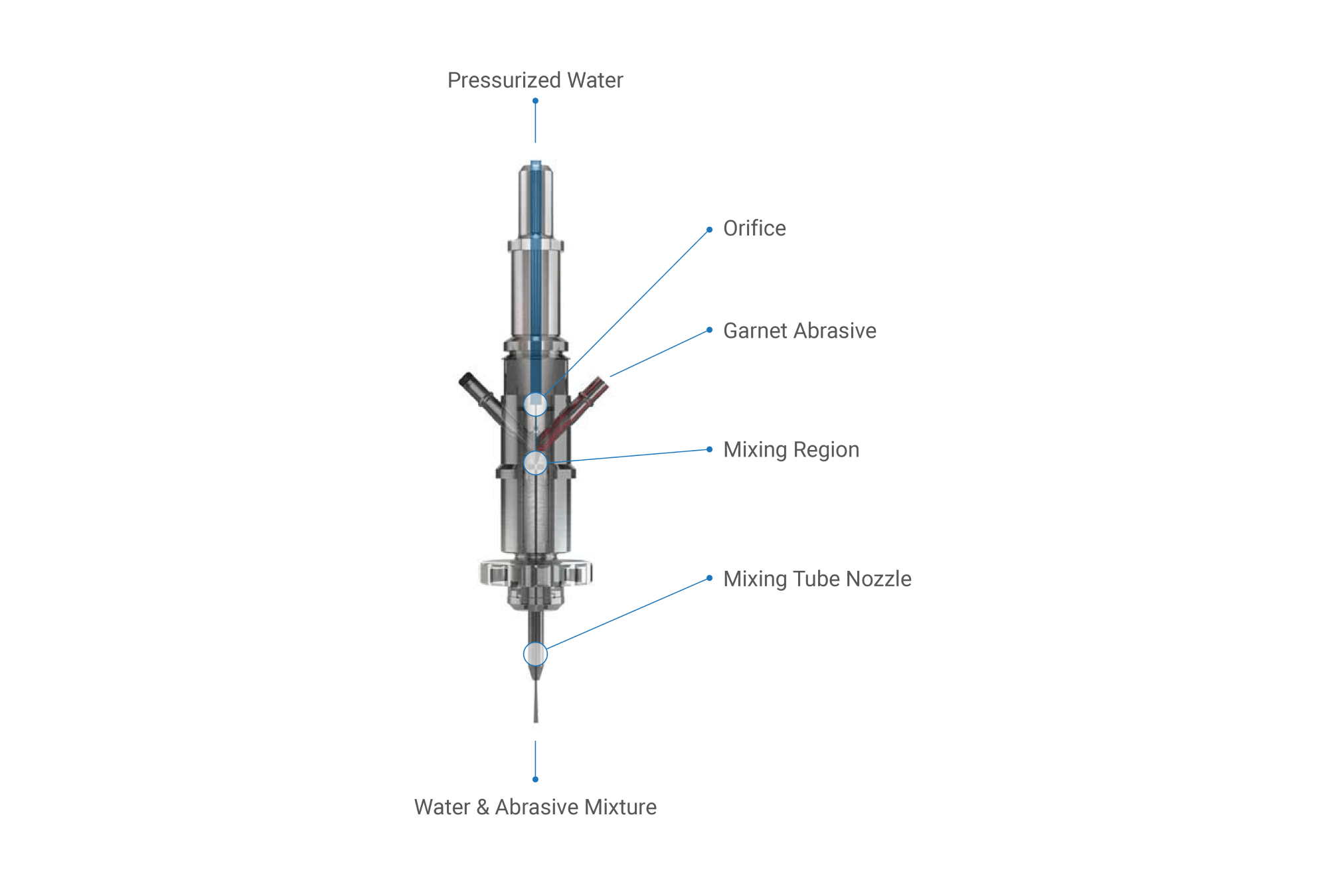
However, there are two limits to the amount of pressure that can be used. The first limit is that water will become ice and cannot be pumped anymore if the pressure reaches 150,000 psi at room temperature. To achieve higher pressures, the water must be heated. The second limit is hardware reliability and economics because higher pressures require stronger materials and better seals.
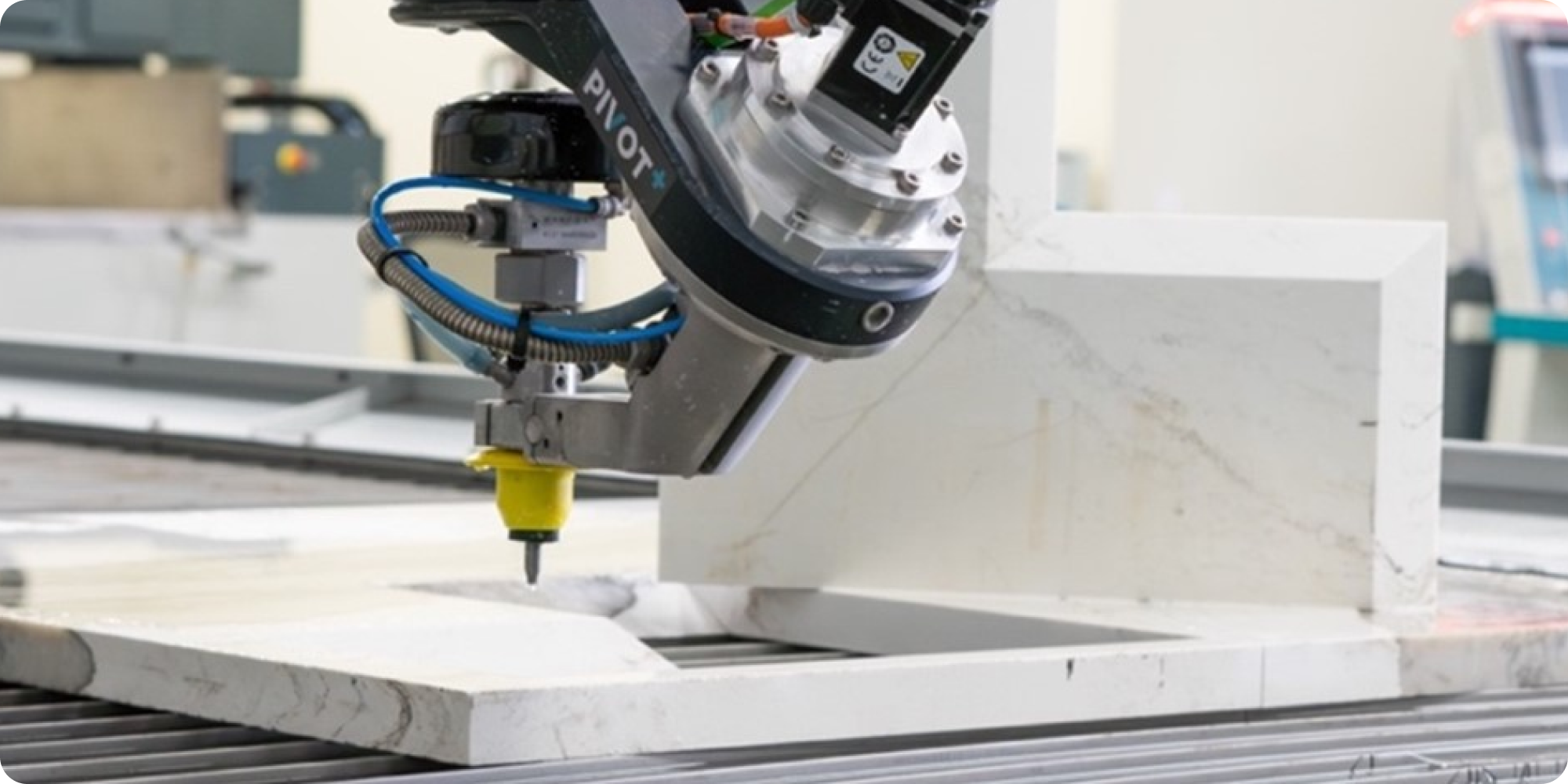
Work Fast, Save Money
As technology advances, we can use higher pressures to achieve higher velocity jets. Water and relatively softer abrasives can penetrate harder materials due to shear rate of impact, or velocity, like how a straw can penetrate a tree in a hurricane. Check out the figure below to see how waterjet velocity can be obtained at different pressures, as well as the abrasive particle velocity if we add 10% abrasives by weight to the waterjet.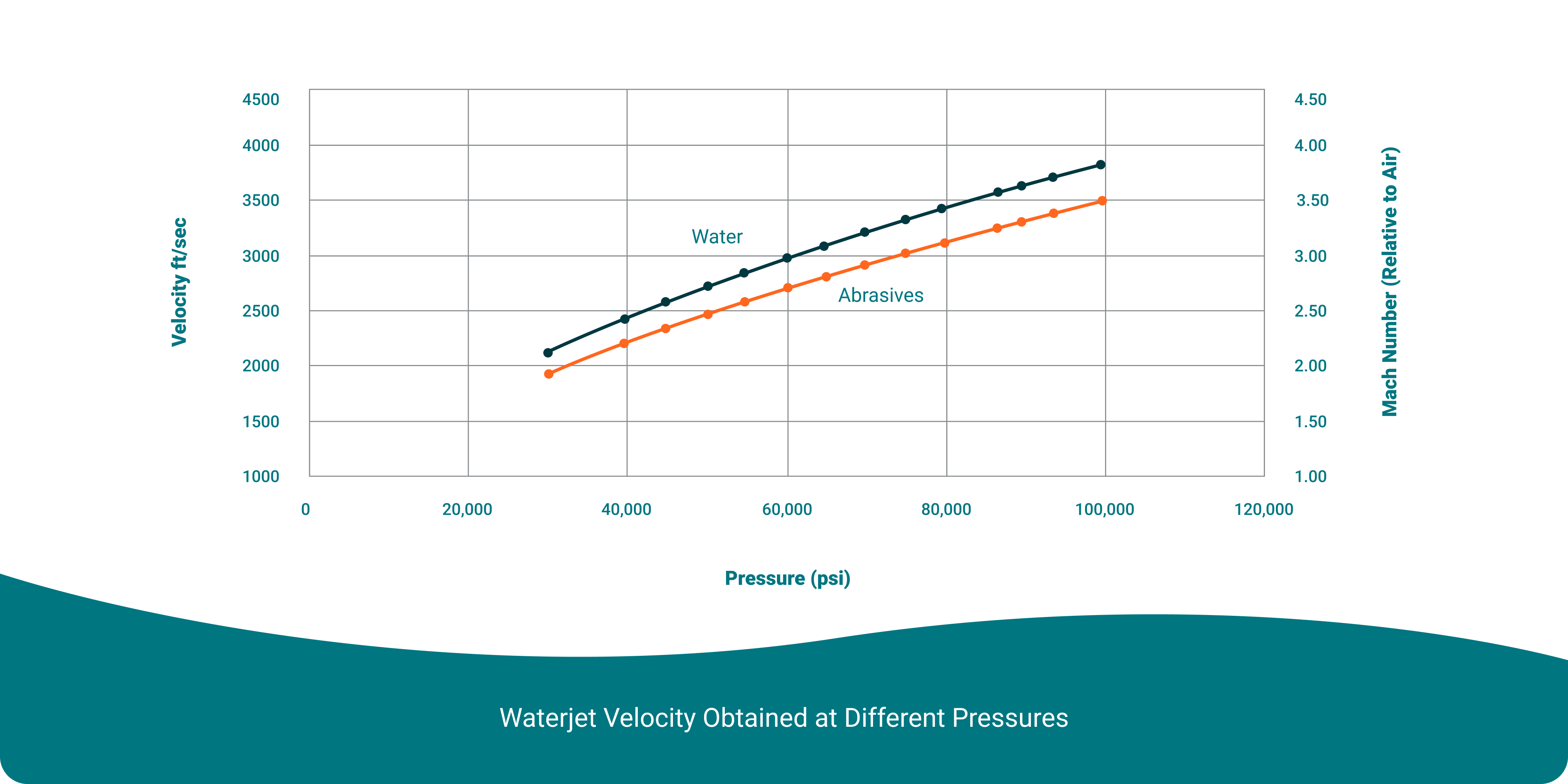
One of the most important motivations to increasing the velocity is to reduce the quantity of abrasives needed, as they are the highest cost item. By increasing the velocity, we will need less mass. On the other hand, if a user wants to operate at lower abrasive velocities (and thus a lower pressure pump), then they must compensate for the reduced velocity by increasing the mass of the abrasives, which will increase operational cost.
With pumps operating reliably at 90,000 psi, increasing abrasive particle velocity is beneficial for reducing consumption, therefore saving money. So next time you go to Home Depot to rent that pressure washer, pick the one with the highest pressure rating. Better yet, if you buy a waterjet machine, buy the one that gives you the highest pressure so you can do your job faster and save on your bills.