Five Waterjet Terms You Should Know
Industry terms are one of the most important things to learn about waterjet technology. Whether you’re new to the world of waterjet, or a seasoned veteran, these five terms are some of the most important to know.
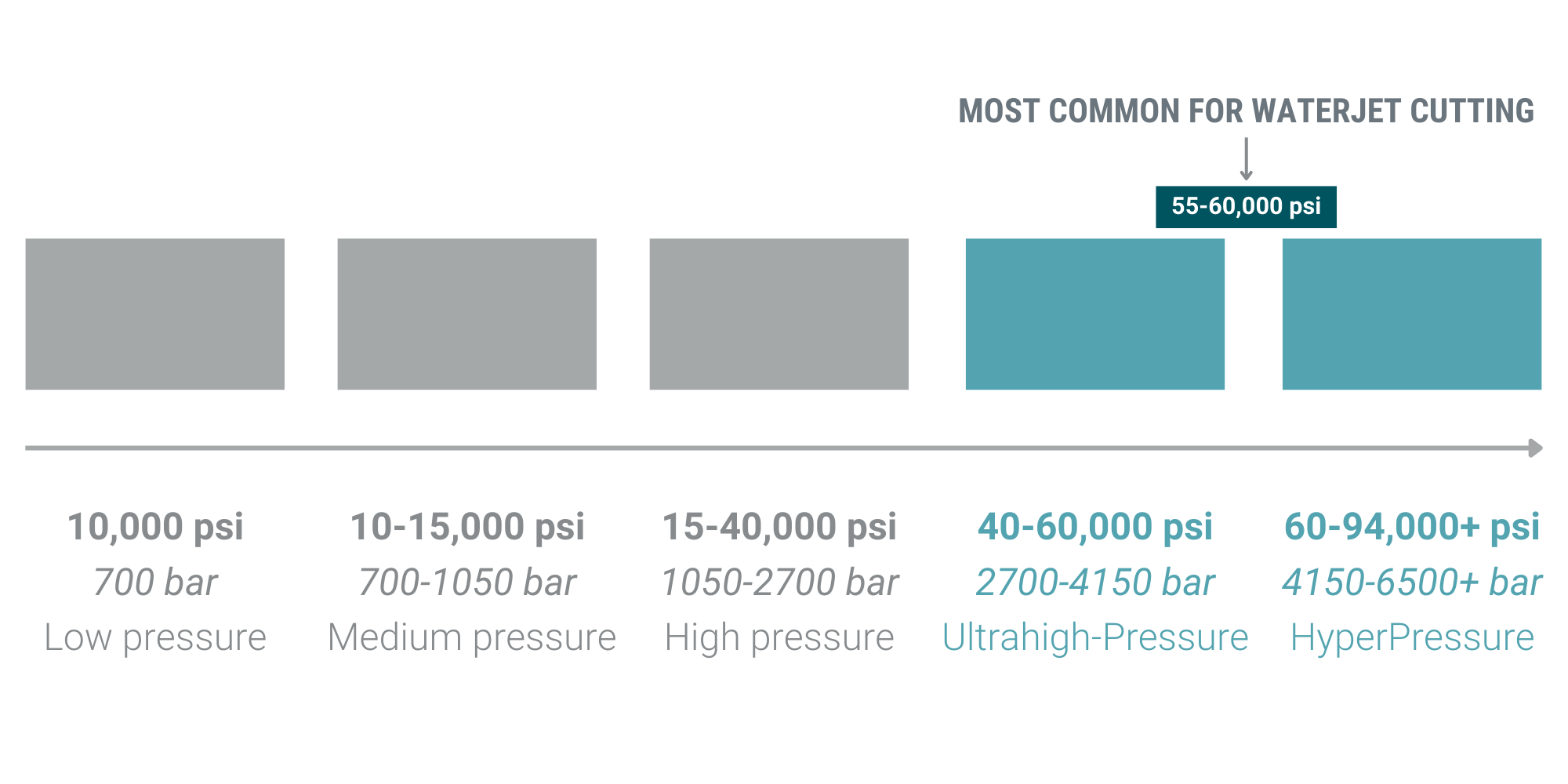
Why does ultrahigh-pressure matter? The industry defines the pressure levels based on the pressure ranges used for high-pressure plumbing. Understanding pump pressure is key to evaluating waterjet technology – it has a huge impact on productivity and cut quality. When you increase the speed of the stream, you increase the efficiency of your cut. (See Stream Velocity below.)
The “intensification principle”, or ratio, uses the difference in biscuit/plunger area to intensify, or increase the pressure. Hydraulic oil is pressurized and the low-pressure oil pushes against a biscuit, which has a face area 20 times greater than the face of the high-pressure plunger that pushes against the water. Therefore, the pressure is “intensified” twenty times. E.g., 3,000 psi of oil pressure will generate 60,000 psi of water pressure due to the 20:1 ratio of biscuit area to plunger area.
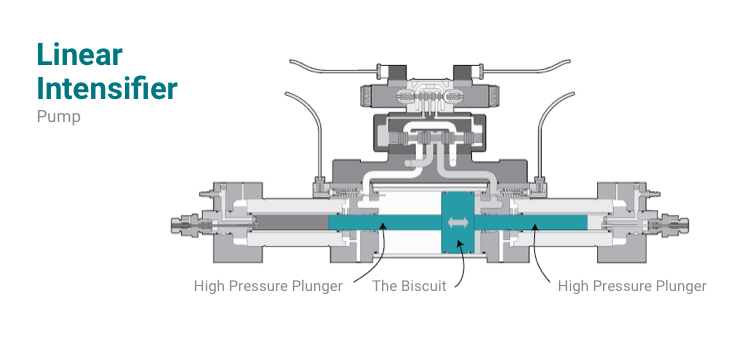
Why are intensifier pumps more common? As waterjet technology has advanced, intensifiers have evolved to meet the demands of high-production environments. They’ve become the more dependable pump option with longer maintenance intervals when compared to a direct drive pump.
Once the stream exits the orifice, it's all about velocity. There is no pressure in the stream after the water passes through the orifice. In abrasive waterjet cutting, the faster the stream, the quicker the abrasive moves, the faster the cutting, the smaller the diameter of the stream, and the less abrasive is required.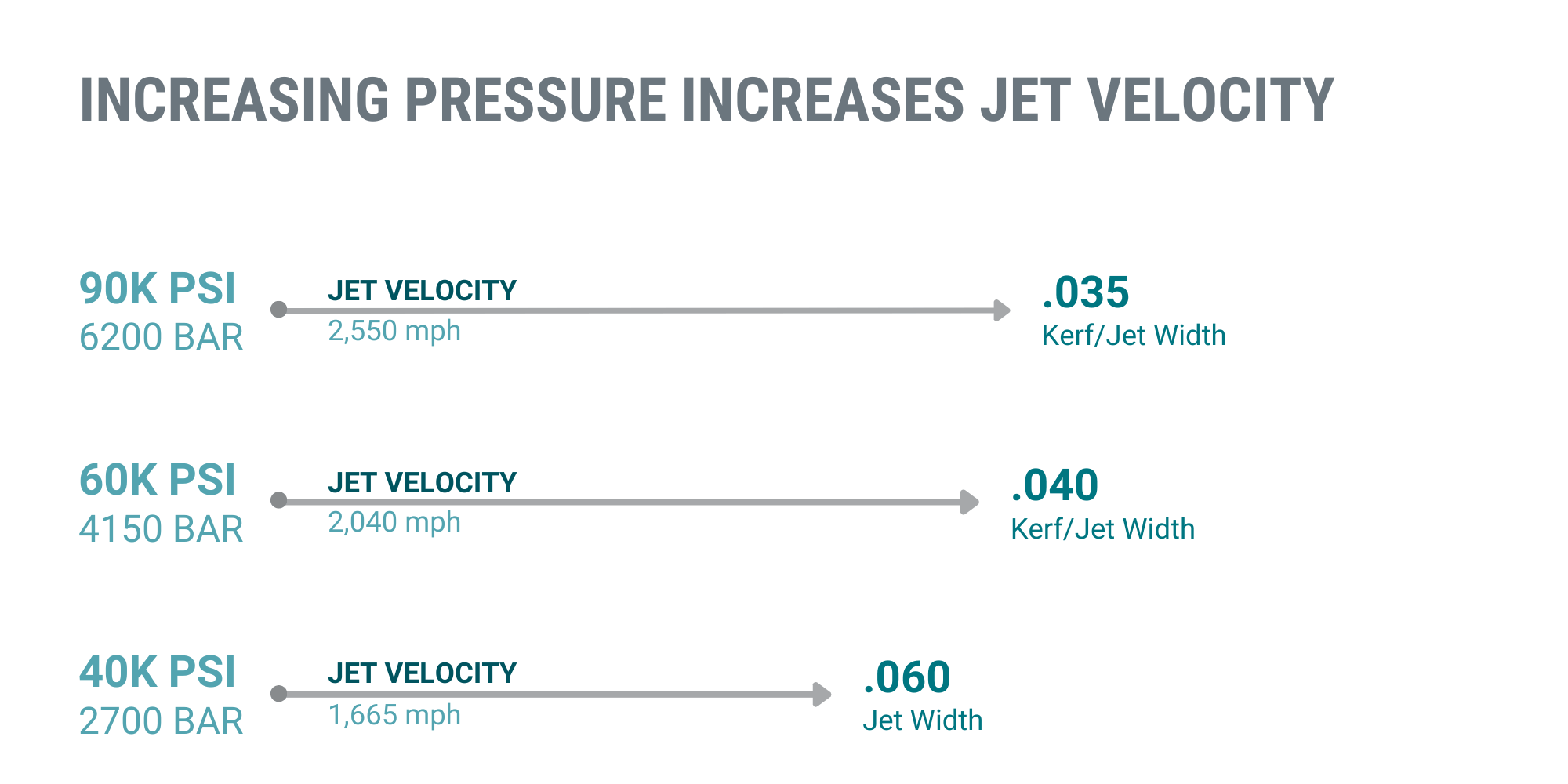
Stream velocity is essentially how a waterjet cuts. Since waterjet is a supersonic erosion process, when you increase the speed of the stream, you increase the efficiency at which you cut. In abrasive waterjet cutting, the faster the stream, the faster the abrasive is moving. This means the stream has a smaller diameter, and less abrasive is required to cut.
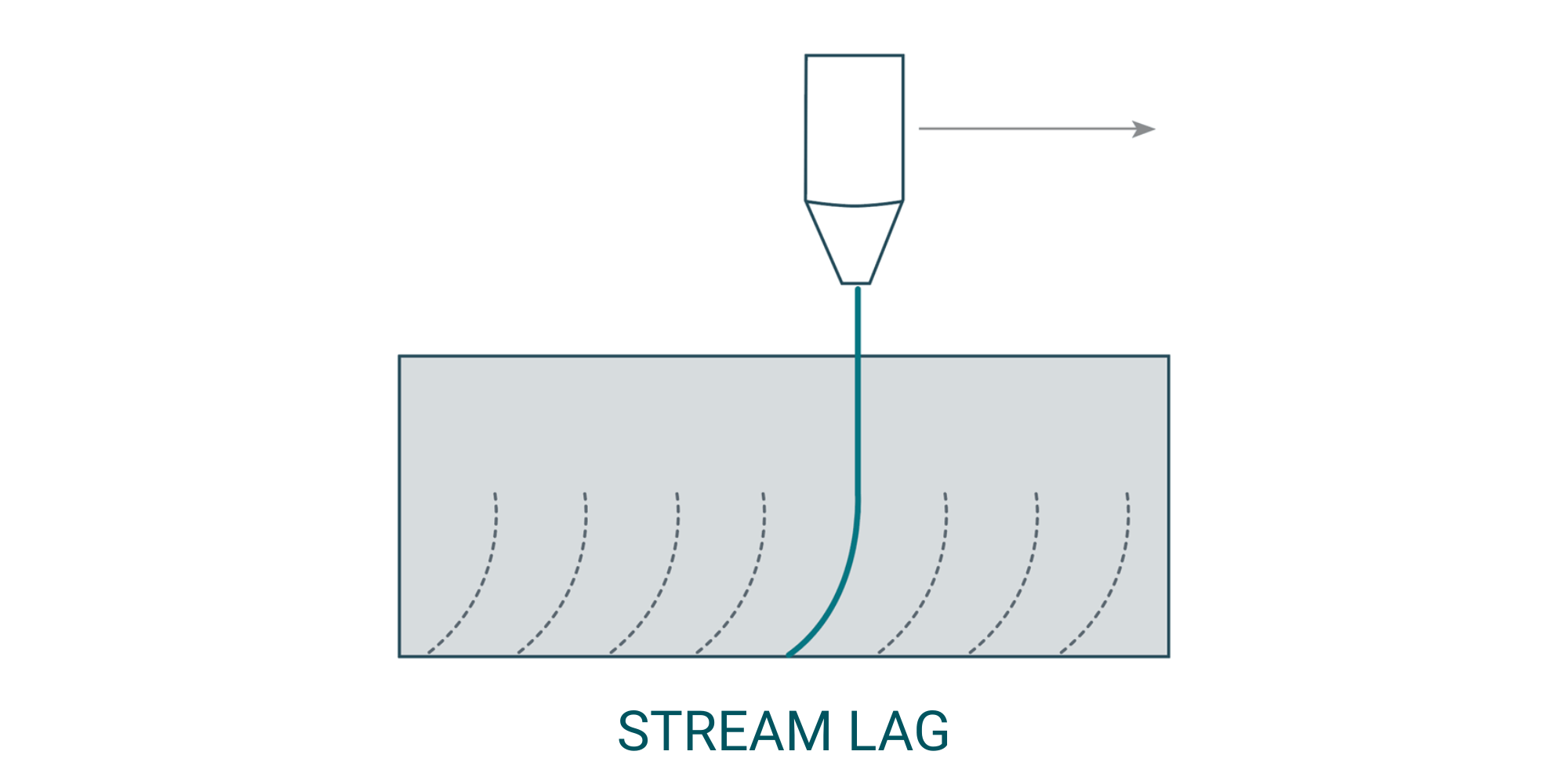
Why is this an important term to know? To prevent stream lag, there are multiple options: reducing your cutting speed and running test cuts to check the tolerance control (which uses more material and time) or utilizing Dynamic Waterjet’s taper compensation capabilities. Dynamic Waterjet uses what is referred to as “lead angle” and points the nozzle forward to help compensate for the jet lag.
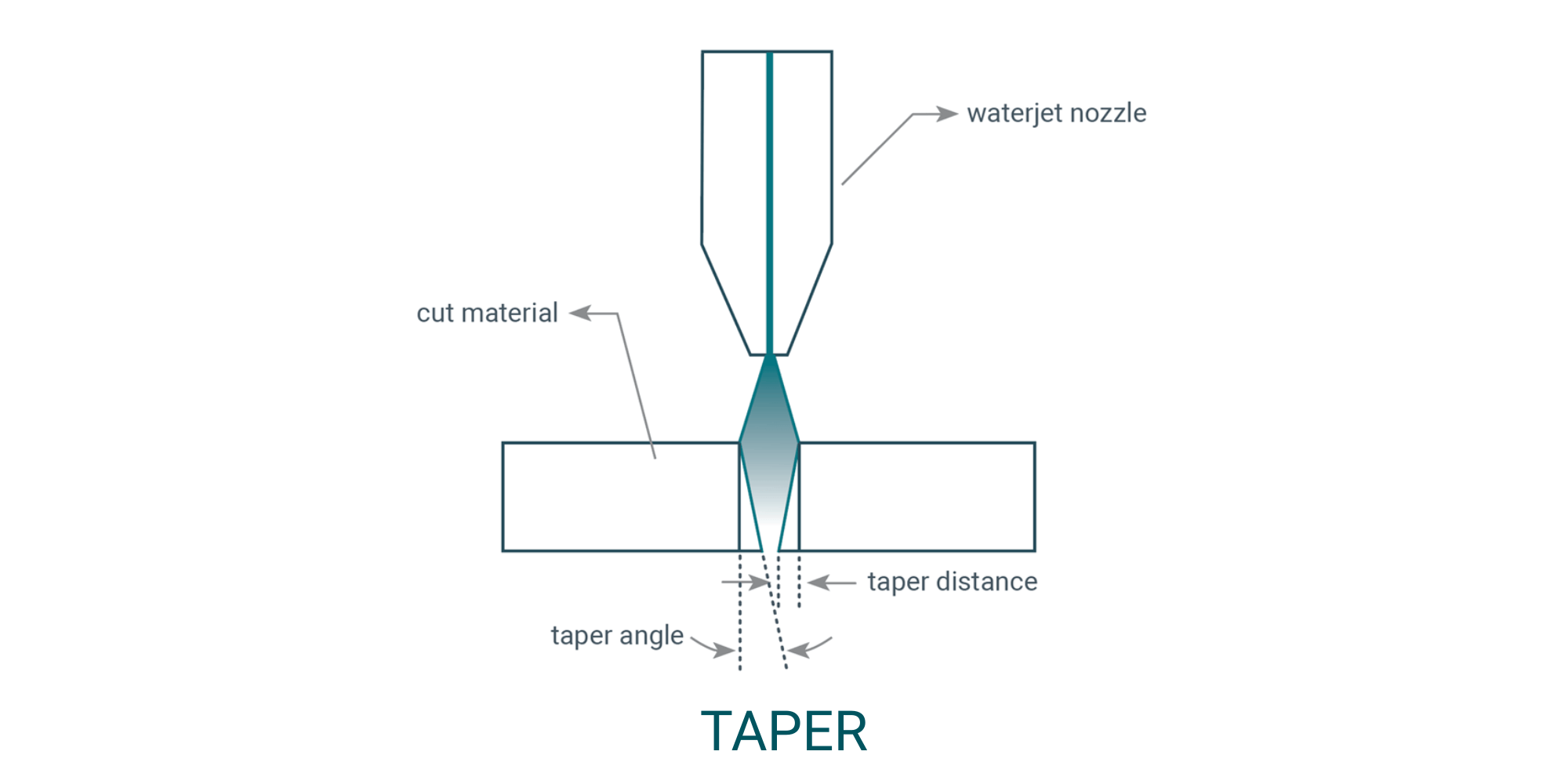
Taper and stream lag go hand-in-hand. While stream lag affects the bottom of the material, taper affects the top of the material where the stream enters. To minimize taper, slowing down your cut speed is recommended. However, we also recommend utilizing Dynamic Waterjet’s taper compensation capabilities.
1. Ultrahigh-pressure (UHP)
The waterjet industry has different definitions for differences in pressure levels. Ultrahigh-pressure is between 40,000 and 60,000 psi. For waterjet cutting, most pumps operate between 55–60,000 psi.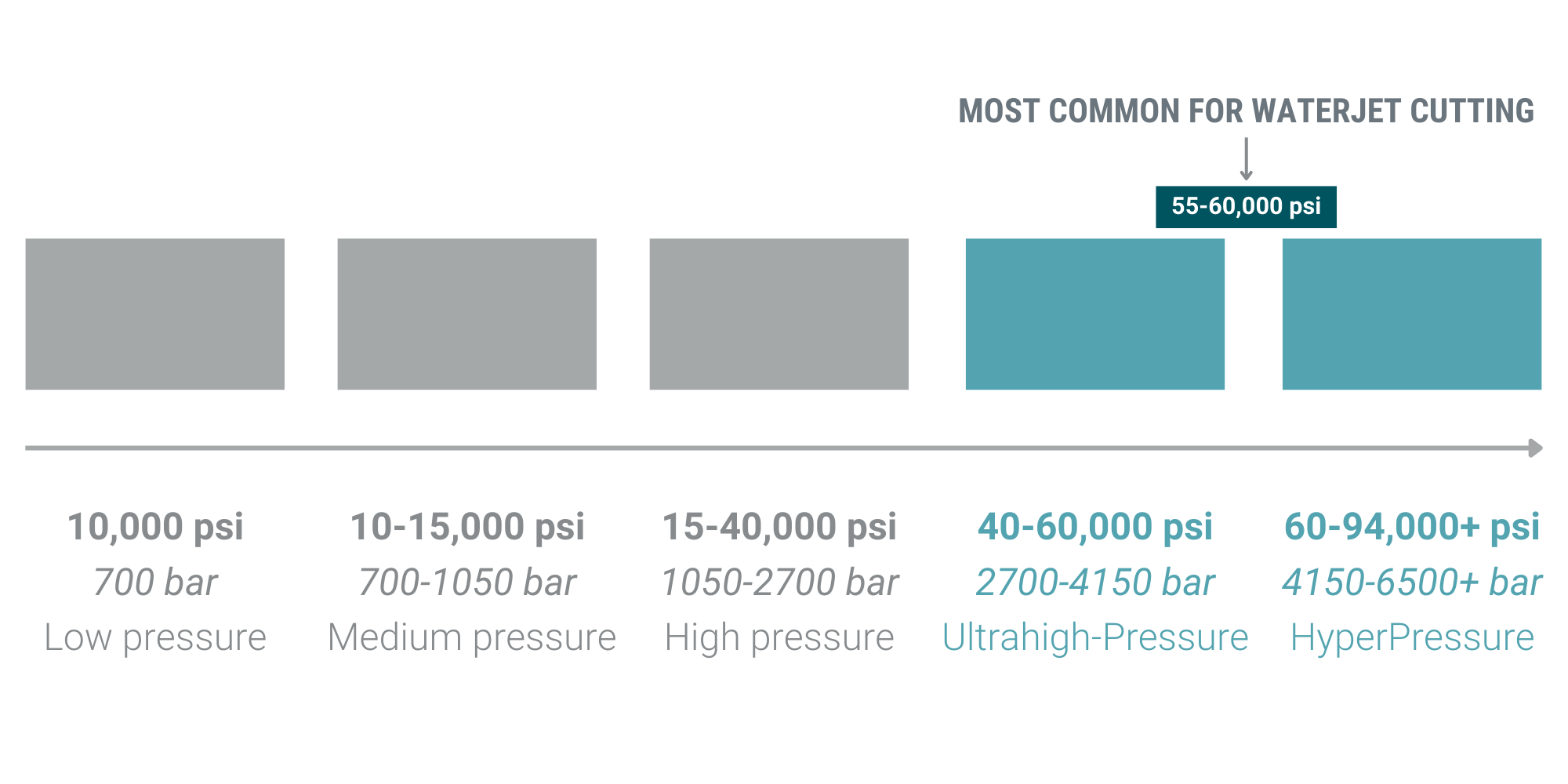
Why does ultrahigh-pressure matter? The industry defines the pressure levels based on the pressure ranges used for high-pressure plumbing. Understanding pump pressure is key to evaluating waterjet technology – it has a huge impact on productivity and cut quality. When you increase the speed of the stream, you increase the efficiency of your cut. (See Stream Velocity below.)
2. Intensifier (Pump)
The linear intensifier pump is the original, and most common technology used in waterjet cutting. Intensifier pumps use the “intensification principle” to pressurize water.The “intensification principle”, or ratio, uses the difference in biscuit/plunger area to intensify, or increase the pressure. Hydraulic oil is pressurized and the low-pressure oil pushes against a biscuit, which has a face area 20 times greater than the face of the high-pressure plunger that pushes against the water. Therefore, the pressure is “intensified” twenty times. E.g., 3,000 psi of oil pressure will generate 60,000 psi of water pressure due to the 20:1 ratio of biscuit area to plunger area.
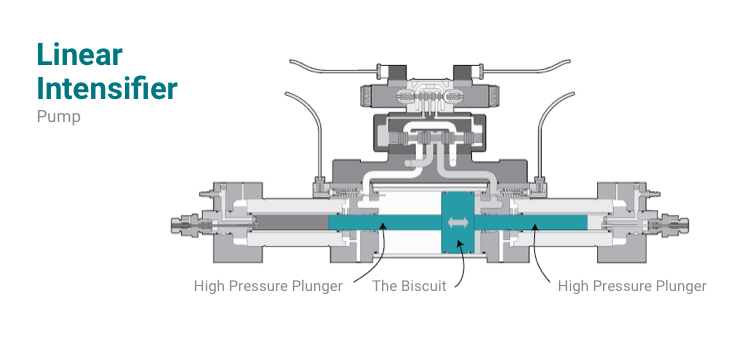
Why are intensifier pumps more common? As waterjet technology has advanced, intensifiers have evolved to meet the demands of high-production environments. They’ve become the more dependable pump option with longer maintenance intervals when compared to a direct drive pump.
3. Stream Velocity
With waterjet cutting, as pressure goes up, the speed of the waterjet stream increases.Once the stream exits the orifice, it's all about velocity. There is no pressure in the stream after the water passes through the orifice. In abrasive waterjet cutting, the faster the stream, the quicker the abrasive moves, the faster the cutting, the smaller the diameter of the stream, and the less abrasive is required.
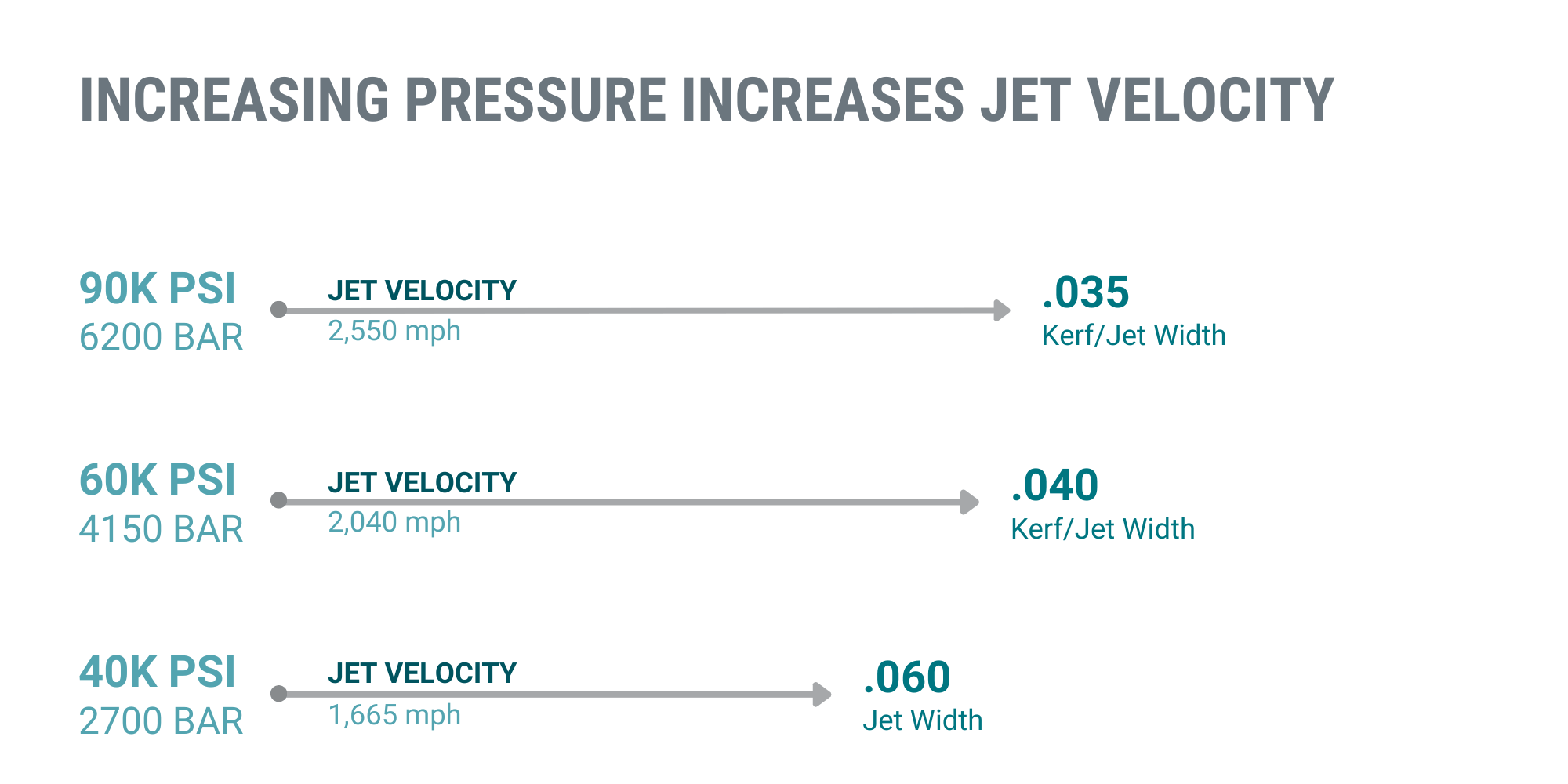
Stream velocity is essentially how a waterjet cuts. Since waterjet is a supersonic erosion process, when you increase the speed of the stream, you increase the efficiency at which you cut. In abrasive waterjet cutting, the faster the stream, the faster the abrasive is moving. This means the stream has a smaller diameter, and less abrasive is required to cut.
4. Stream Lag
Stream lag is a deflection of a pure waterjet or abrasive waterjet caused by cutting material; the exit point of the stream at the bottom of the material trails behind the entrance point of the stream at the top of the material. The faster material is cut, the greater the stream lag. Typically stream lag is exhibited when cutting occurs at 25% of maximum cut speed or greater. Below 25% the stream is very close to vertical.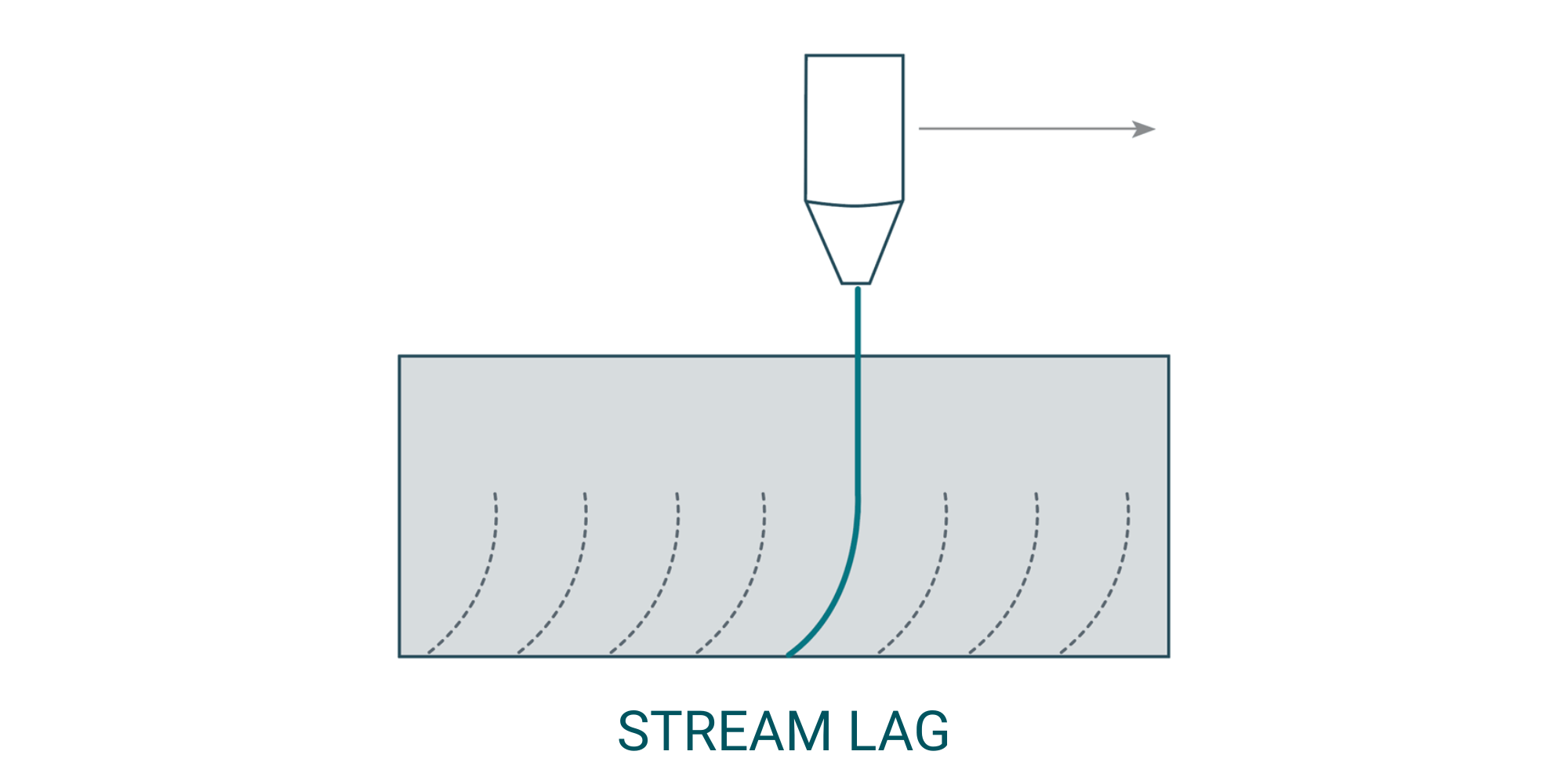
Why is this an important term to know? To prevent stream lag, there are multiple options: reducing your cutting speed and running test cuts to check the tolerance control (which uses more material and time) or utilizing Dynamic Waterjet’s taper compensation capabilities. Dynamic Waterjet uses what is referred to as “lead angle” and points the nozzle forward to help compensate for the jet lag.
5. Taper
Taper in waterjet cutting pertains to non-straight kerf walls. Kerf taper is most common in abrasive waterjet cutting, as opposed to pure waterjet cutting. When cutting material, the top of the cut is often wider than the bottom of the cut, yielding a V-shaped taper. Slow down cut speed to minimize taper. Even below 20% of maximum cut speed the kerf will usually still exhibit some taper.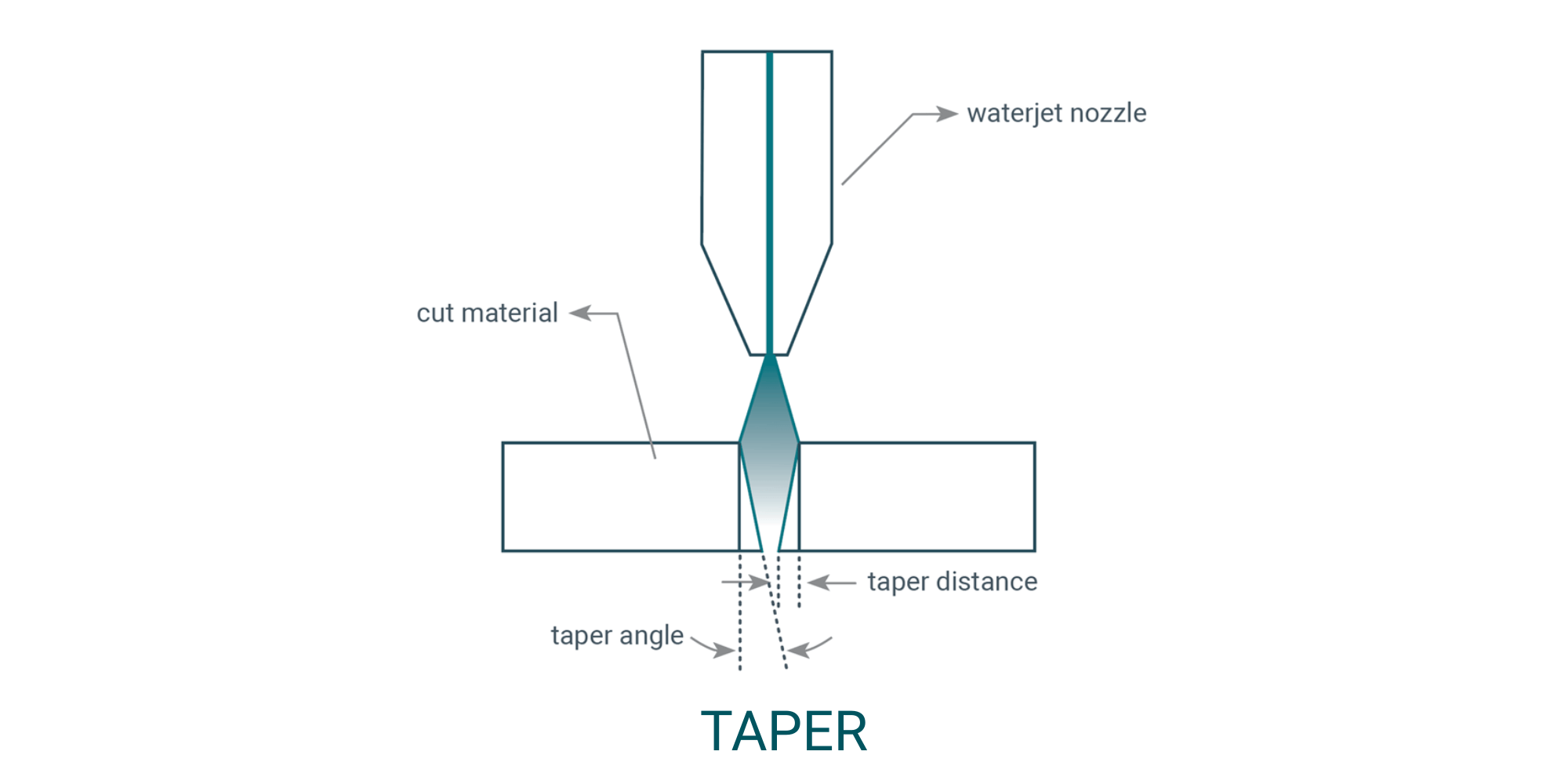
Taper and stream lag go hand-in-hand. While stream lag affects the bottom of the material, taper affects the top of the material where the stream enters. To minimize taper, slowing down your cut speed is recommended. However, we also recommend utilizing Dynamic Waterjet’s taper compensation capabilities.