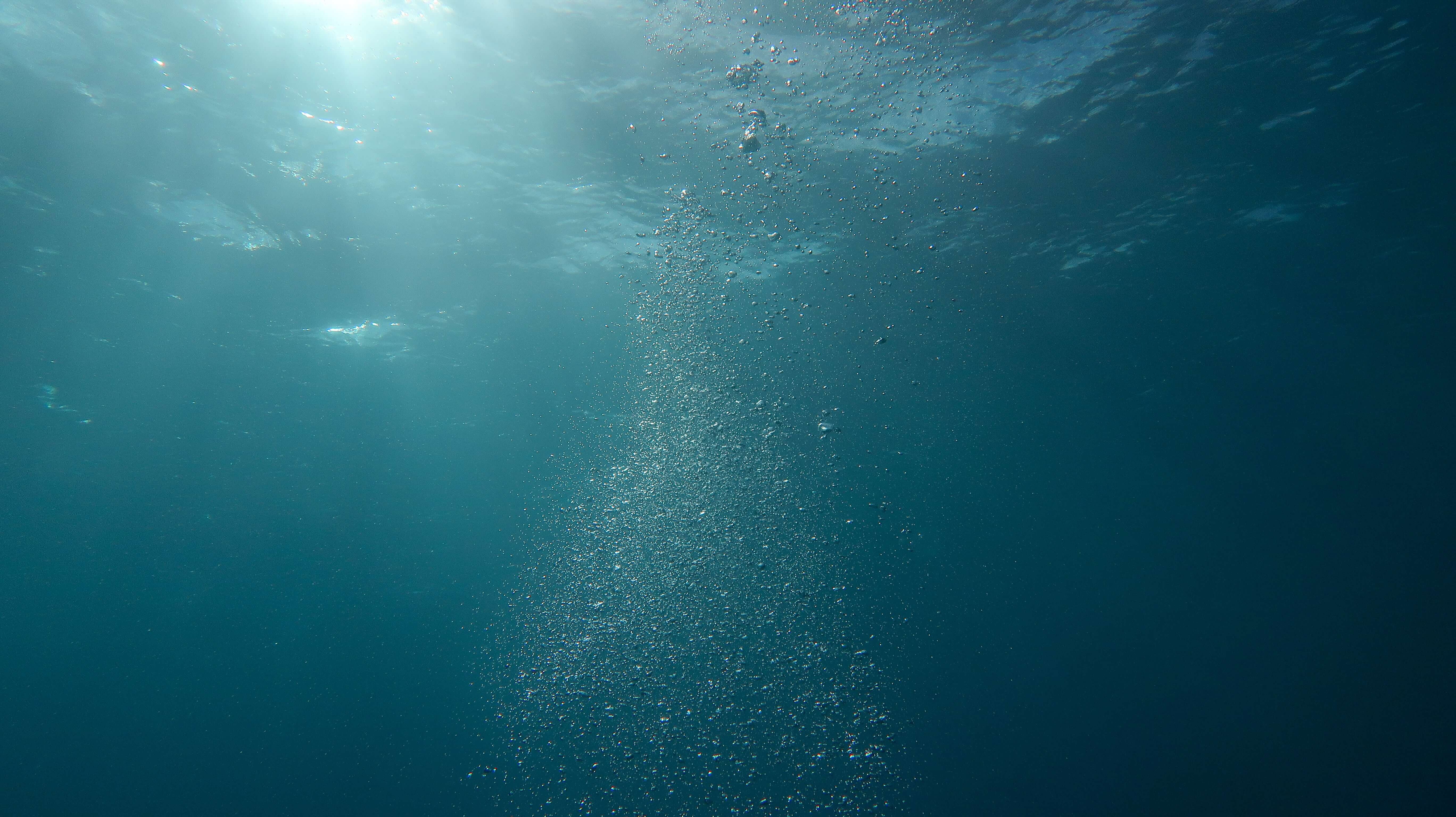
Waterjet Library
A growing selection of articles, customer stories, videos, eBooks, and more that are designed to assist you on your waterjet technology journey.
A growing selection of articles, customer stories, videos, eBooks, and more that are designed to assist you on your waterjet technology journey.